Streamlining Manufacturing Success with Strategic Alignment
Automotive Manufacturing
The Challenge
The Problem: The manufacturing company’s manufacturing facility faced mounting pressure to increase piston production to keep up with global automotive demand. Inefficiencies in production, compounded by outdated equipment and insufficient workforce training, were hindering their ability to meet market expectations. To overcome these challenges, Manufacturing Company partnered with InSync Training to design a strategic approach that aligned learning and development initiatives with business objectives.
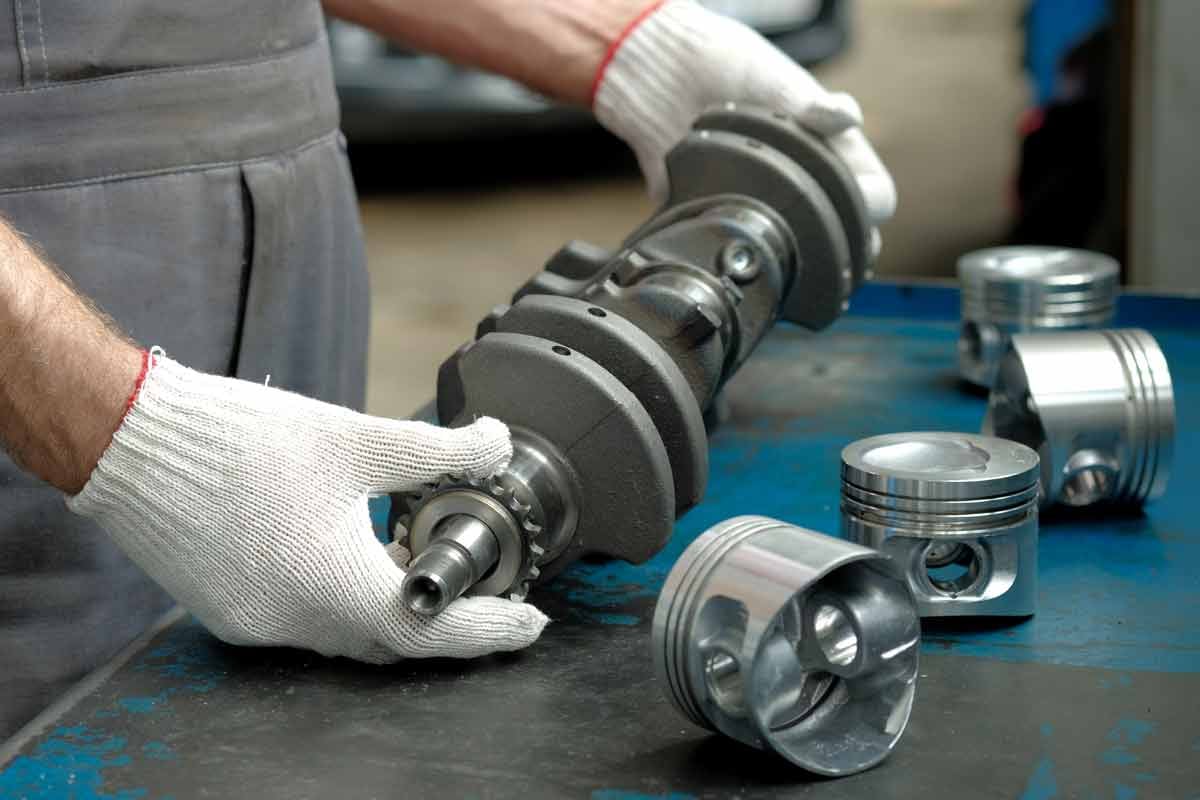
CHALLENGES WE IDENTIFIED
-
Operational Inefficiencies: Bottlenecks and outdated production processes slowed overall output.
-
Limited Workforce Training: Employees lacked the skills needed to adapt to modern manufacturing requirements.
-
Outdated Machinery: Aging equipment contributed to inefficiencies and reduced productivity.
Our Approach
InSync Training collaborated with the company to address these challenges through a multi-pronged strategy:
-
Strategic Alignment Implementation
- Identified business objectives to increase piston production by 20% within the next fiscal year.
- Conducted detailed analysis of production data to pinpoint inefficiencies and outdated practices.
- Identified business objectives to increase piston production by 20% within the next fiscal year.
-
Targeted Training Programs
- Designed specialized training programs focusing on machine operation, maintenance, and lean manufacturing principles.
- Combined theoretical instruction with hands-on application to empower employees on the production floor.
- Designed specialized training programs focusing on machine operation, maintenance, and lean manufacturing principles.
-
Upgrading Machinery and Optimizing Production Schedules
- Invested in state-of-the-art machinery to enhance production capabilities.
- Adjusted work schedules to maximize production hours while maintaining employee morale through flexible shift options.
- Invested in state-of-the-art machinery to enhance production capabilities.
-
Performance Metrics Integration
- Linked training outcomes to performance evaluations, ensuring accountability and recognizing achievements.
- Implemented career advancement opportunities tied to skill development and operational improvements.
- Linked training outcomes to performance evaluations, ensuring accountability and recognizing achievements.
-
Continuous Feedback and Improvement
- Established regular feedback loops using employee surveys and focus groups to refine training programs.
- Monitored machinery performance and training effectiveness to ensure sustained success.
- Established regular feedback loops using employee surveys and focus groups to refine training programs.
Our Approach
InSync Training collaborated with the healthcare technology company to design and implement a customized virtual training program through a multi-faceted approach:
-
Strategic Realignment and Stakeholder Engagement
- Worked with stakeholders to identify specific training needs and skill gaps in MRI/CT operations and IT systems.
- Established alignment between training objectives and broader organizational goals for operational efficiency and patient care quality.
- Worked with stakeholders to identify specific training needs and skill gaps in MRI/CT operations and IT systems.
-
Designing Comprehensive Training Modules
- Developed interactive modules focused on critical technical competencies, including equipment operation, maintenance, and patient care protocols.
- Ensured alignment with the latest healthcare practices and technology standards to future-proof training content.
- Developed interactive modules focused on critical technical competencies, including equipment operation, maintenance, and patient care protocols.
-
Integrating Hands-on Practice:
- Facilitated hands-on practice sessions in a virtual environment, allowing trainees to work directly with realistic equipment simulations.
- Incorporated video demonstrations and live guidance from proctors to enhance practical skill application.
- Facilitated hands-on practice sessions in a virtual environment, allowing trainees to work directly with realistic equipment simulations.
-
Practical skill application. Feedback and Continuous Improvement Mechanisms
- Established feedback loops through surveys and assessments to measure training effectiveness.
- Used insights to refine content and delivery methods continuously, ensuring relevance and engagement
- Established feedback loops through surveys and assessments to measure training effectiveness.
The Results
Exceeded Production Goals:
Piston production increased by 25% within one year, surpassing the initial goal of 20%.
Enhanced Employee Engagement:
Workforce engagement increased by 20% as employees felt more skilled and valued in their roles.
Improved Efficiency:
Streamlined processes and modernized equipment boosted overall operational performance.
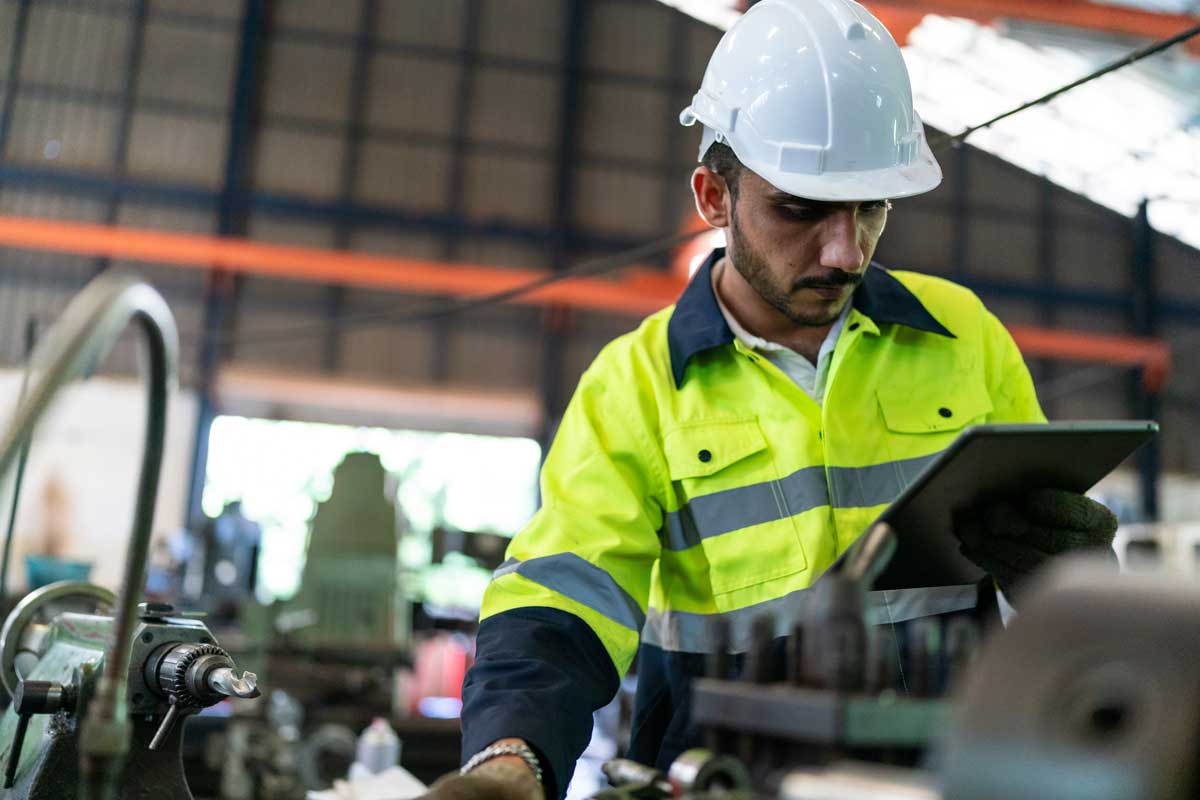
Actionable Advice:
Steps to Cultivate Continuous Learning
- Conduct a Skills Gap Analysis: Identify current and future skill needs through comprehensive analysis.
- Promote a Culture of Lifelong Learning: Communicate benefits of continuous learning through various channels.
- Develop Diverse and Flexible Learning Programs: Offer microlearning, virtual courses, workshops, and peer-to-peer sessions.
- Leverage Technology: Integrate virtual classrooms and collaborative software for enhanced learning experiences.
- Create Practical Application Opportunities:
Establish virtual labs and cross-functional teams for hands-on learning. - Implement Feedback Mechanisms: Gather employee feedback through surveys and performance reviews.
- Measure and Communicate Success: Use KPIs to assess learning impact and share achievements transparently.
Why Partner with InSync Training?
Let’s Build Something Together
Want to optimize your workforce and operations like this manufacturing company? InSync Training offers comprehensive solutions, from training programs to performance analytics, ensuring alignment with your business objectives.
today and see the measurable difference.
.